Our sustainability target to zero CO2 emissions in cement industry
Cement production consumes significant amounts of energy and natural resources, and accounts for approximately 7%of global man-made greenhouse gas (GHG) emissions in CO2 equivalents. (IEA,2018) As it is known Process related CO2 emissions are unavoidable in the cement industry Indirect emissions are produced by burning fossil fuels to heat the kiln. Kilns are usually heated by coal, natural gas or oil, and the combustion of these fuels produces additional CO2 emissions, just as they would in producing electricity. Finally, the electricity used to power additional plant machinery, and the final transportation of cement, represents another source of indirect emissions and account for 5-10 percent of the industry’s emissions. As the “DAL” group, we follow global climate sustainability actions and want to be a supporter of a livable future. we support the “business ambition for 1.5 ͦC” global climate targets and we are starting to include the application of the roadmap determined by the “science-based targets initiative SDG” into our working methods. We are preparing an action plan in line with the goal of reducing CO2 emissions by 55 percent in 2030 and to zero in 2050. We aim to reach the global climate plan targets by increasing the use of waste fuel and increasing energy efficiency. For this purpose, we are turning to modifications that will increase waste fuel burning efficiency. To reduce CO2 emissions in this industrial sector, different studies are ongoing in several areas, including:
- Alternative fuels & raw materials usage;
- Maximizing AF usage in pyro system up to 90%
- Activated clay or equivalent material for clinker substitution
- Energy efficient Pyro-System and Cement plants
- Minimizing heat demand of pyro system
- Electrical efficient process design
- Tubular heat exchanger for calcination
- Avoiding usage of cyclones to preheat material and possibility of calcination without direct heating. Pure CO2 capture, reduced gas handling requirement, smaller kilns and PH tower requirement.
- Waste to Electricity through Oxy-Fuel Combustion
- A conceptual study; 90 % AF firing, high waste energy through clinker cooler to electricity, reducing electrical requirement of the plant to 0 kWh/t clinker production with much lower heat consumption.
- Carbon capture, utilization and storage
- DAL is working on different Carbon Capture technologies in long term to put into the market.
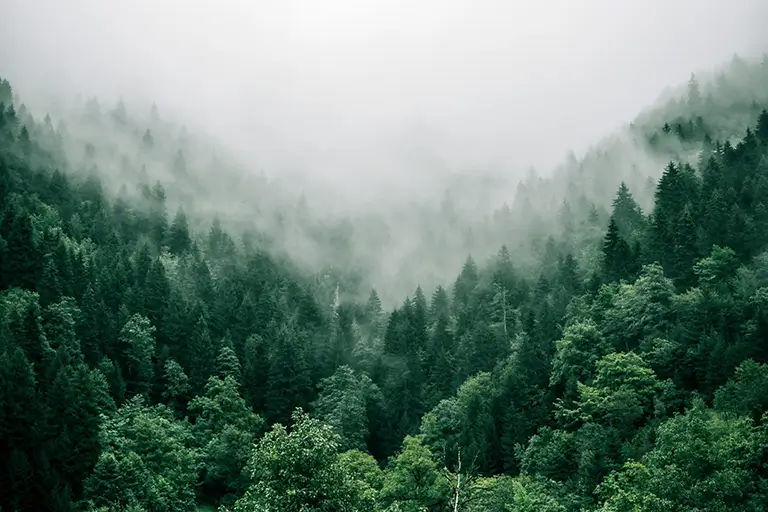